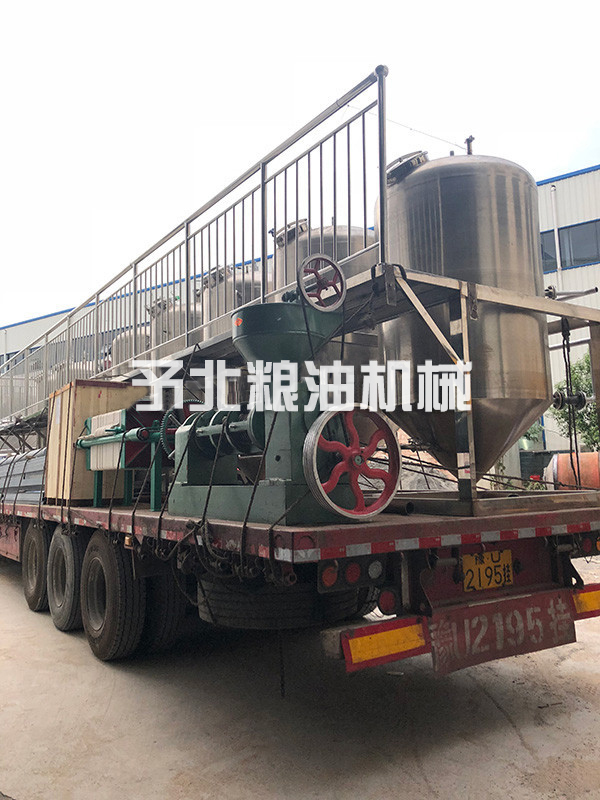
Foreign inspection
Hello, welcome to the official website of Henansheng Yubei Grain and Oil Machinery Co., Ltd.
Product Center
Henan Yubei Grain and Oil Machinery Co., Ltd.
Specializing in products and skilled in technology
Engaged in engineering design and equipment for grain and oil processing and comprehensive utilization of by-products
A complete set of engineering and technical services related to manufacturing, engineering installation, technical training, etc.
Why chooseUs
We are manufacturers, there is no price difference, we can achieve low prices! We use high-quality manufacturing materials to provide customers with reliable products.
Advanced technology We have our own research and development team to ensure our technology progressiveness. Our team has over 10 years of installation experience to ensure quality.
After sales service, all products have a one-year warranty and lifelong free technical guidance. We have a customer service team who provides 24-hour service
Henan Yubei Grain and Oil Machinery Co., Ltd. is an independent legal entity specializing in the production of complete sets of oil machinery equipment, integrating scientific research, manufacturing, and sales The company is mainly engaged in engineering design, equipment manufacturing, engineering installation, technical training, and other related comprehensive engineering and technical services for grain and oil processing and by-product utilization. The company takes the development of professional quality oil engineering as its responsibility, and has long-term cooperation with Henan Higher Education Institutions and Oil Design and Research Institute. The company has a professional technical team, advanced processing technology, main processing equipment, and workshop lifting equipment, and actively learns advanced technology from both domestic and foreign countries......
About Us Honor Case